BATTERY FAILURE CHAMBER
BEAMTIME EDITION - SERIES II
Main metal enclosure designed to control and contain battery failure experiments, whilst capturing in-situ 3D microstructural data via. X-ray imaging.
Second enclosure designed for diffraction (XRD) studies to monitor the phase consistution and crystalline structure of the battery's materials before and after failure.
This chamber was used by the Zero Institue at Oxford University to capture high-speed X-ray images at Diamond Light Source (DLS).
Battery failure can be instigated through electrical failure and/or controlled-heating programmes whilst performing acoustic/ultrasound diagnostics and capturing electrical performance data.
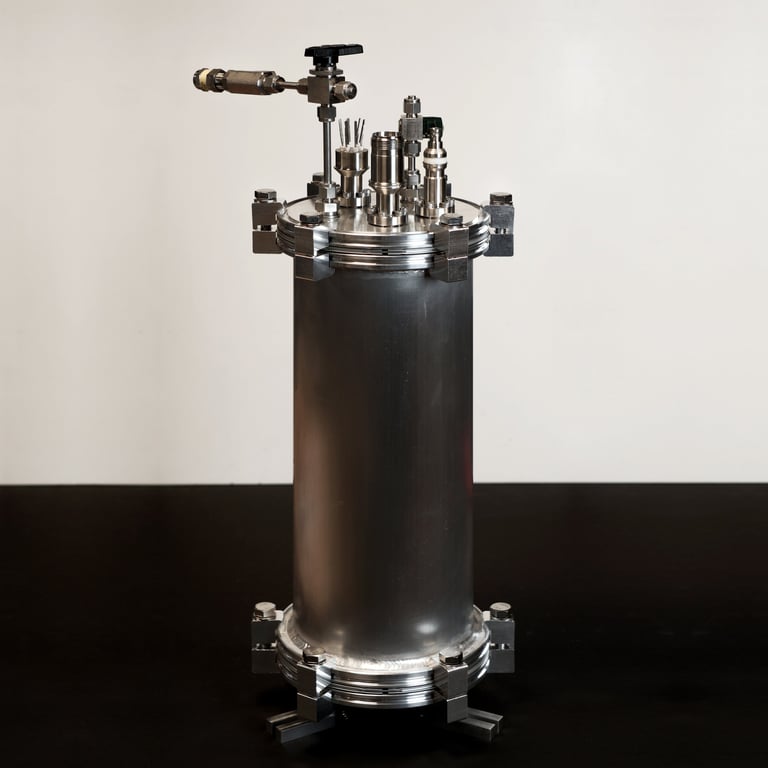
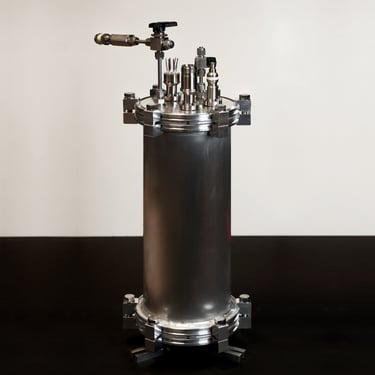
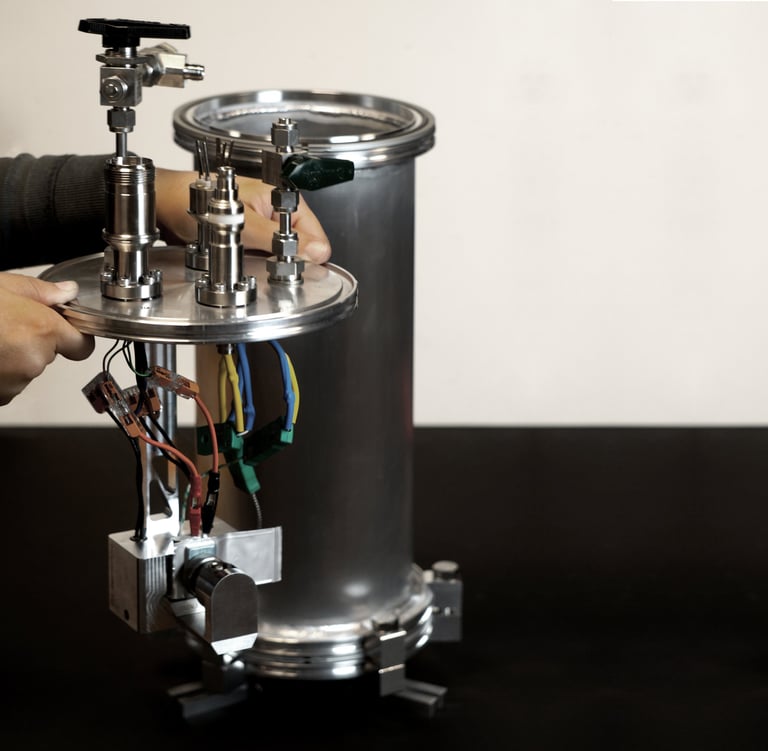
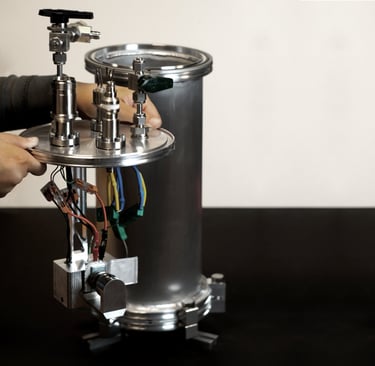
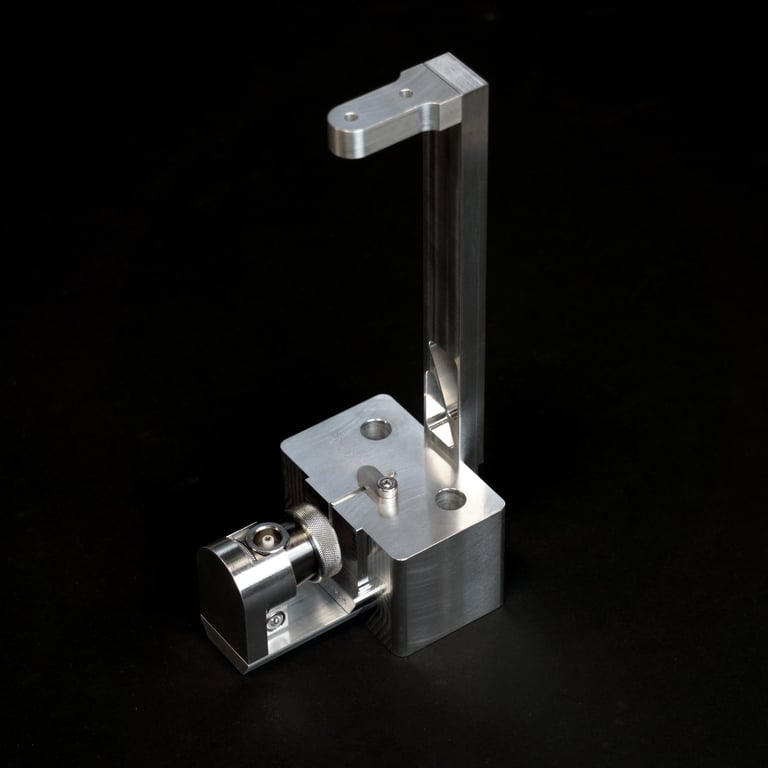
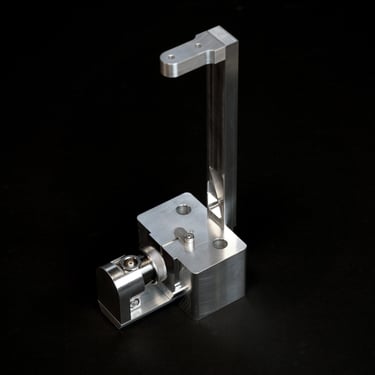
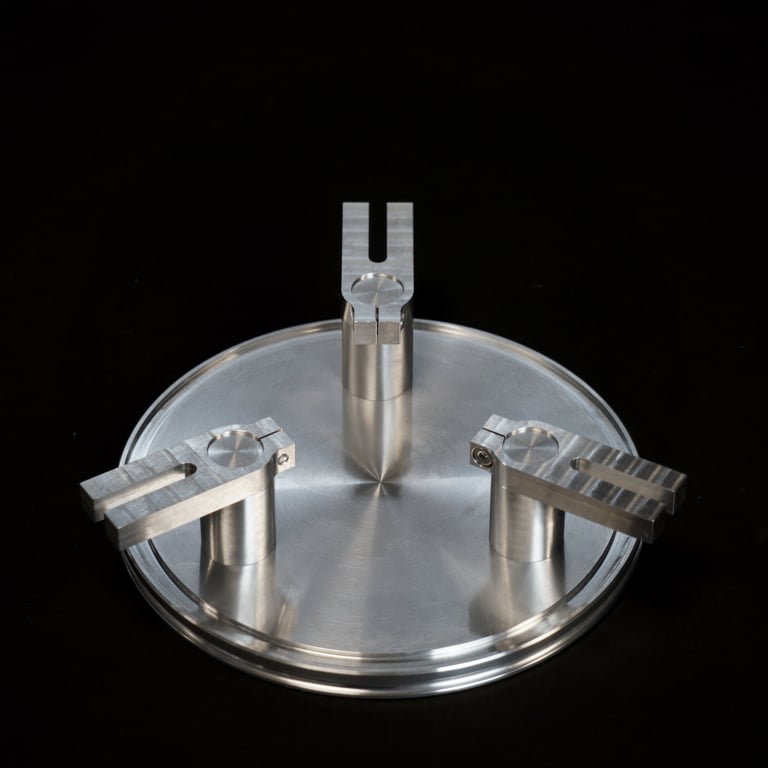
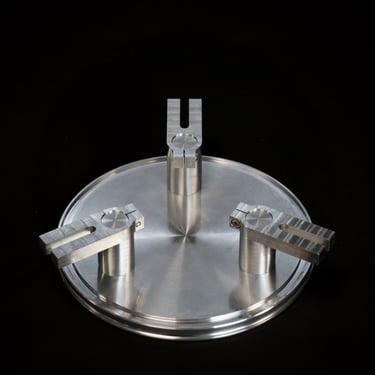
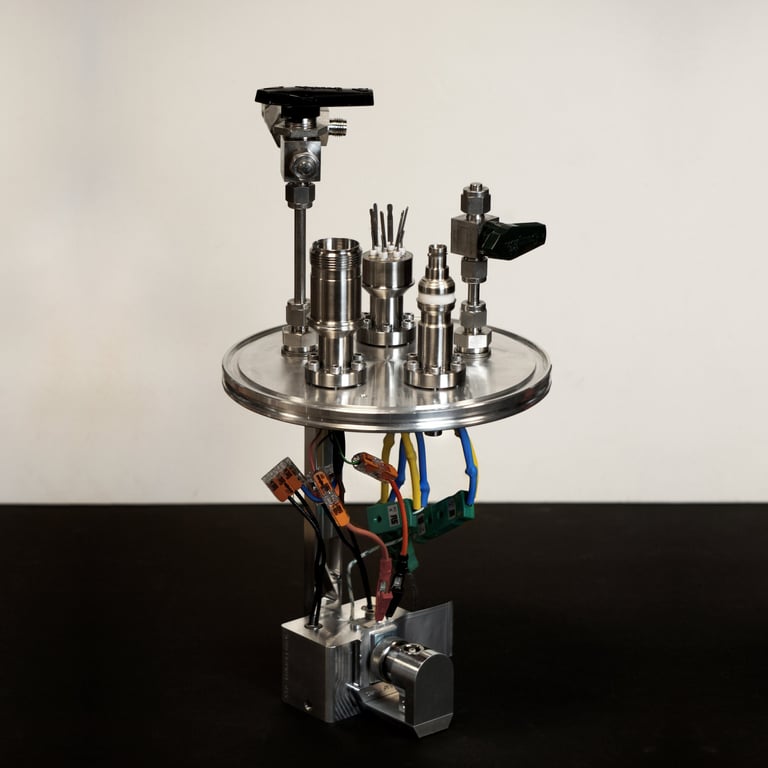
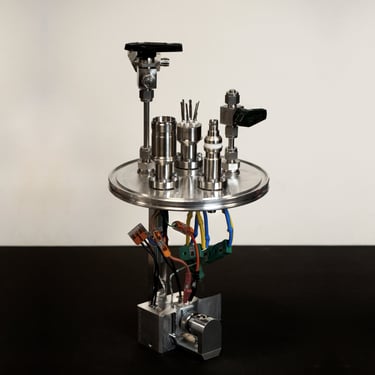
Sealed enclosure to withstand and contain battery failure
Battery electrical contacts for charge/discharge and electrochemical testing
3x thermocouple inputs
Programmable heating
Acoustic/Ultrasound diagnostics
Gas ports for sampling and purging
SPECIFICATION
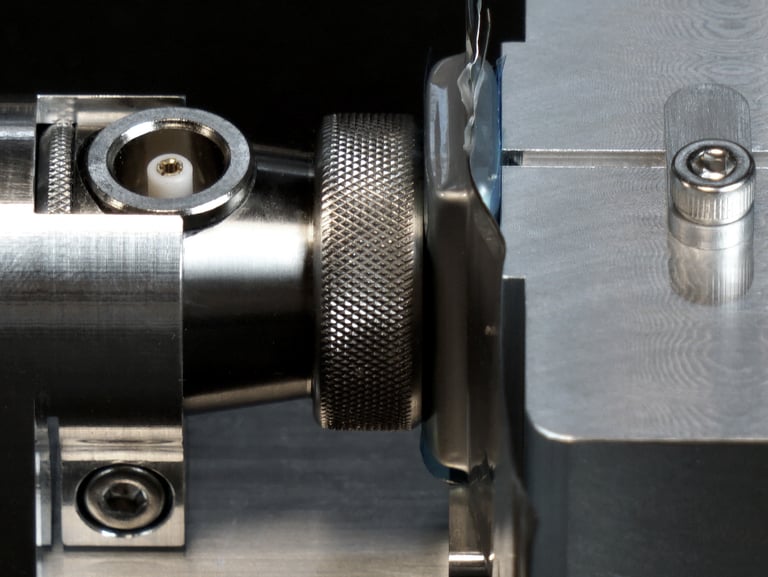
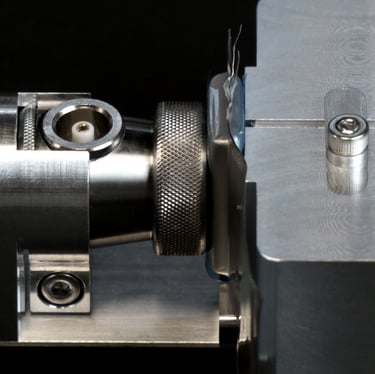
Tubular design with all electrical and gas connections assembled to the lid
Gasket flange design for fast battery changes
Simple disassembly for easier cleaning
Customisation possible with experiment requirements
BATTERY CHAMBER
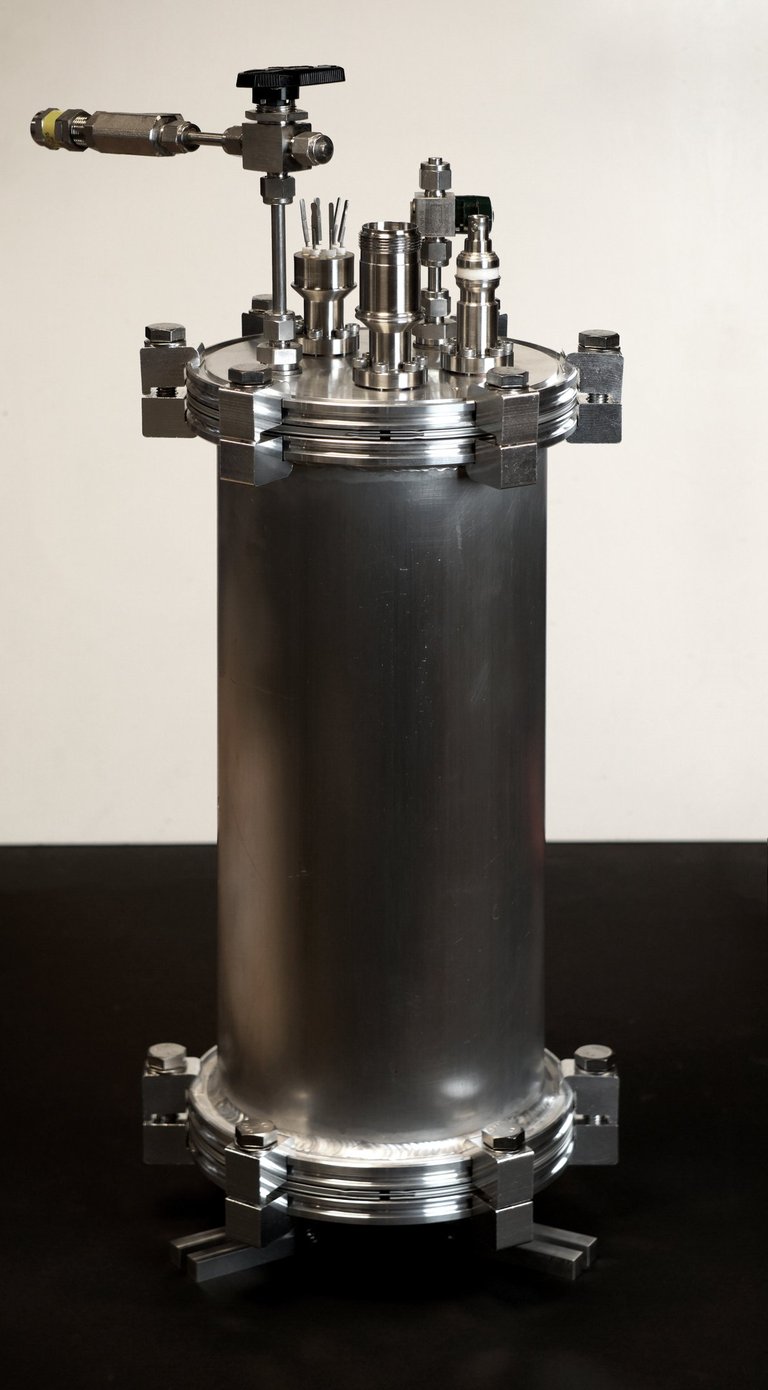
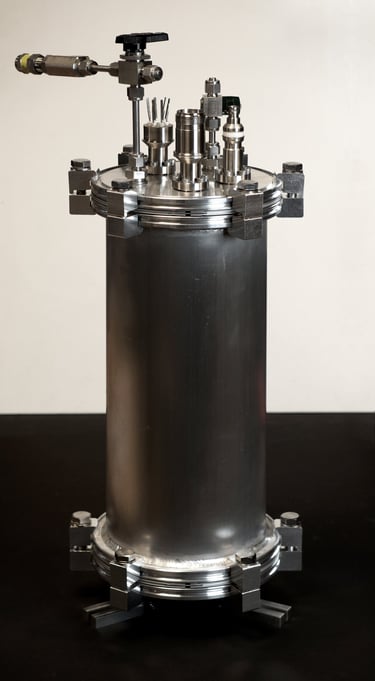
FABRICATION
Aluminium construction for X-ray transmission
Individual holders for acoustic transducers - adjustable compression against the battery
Swivel feet to match stage fixings
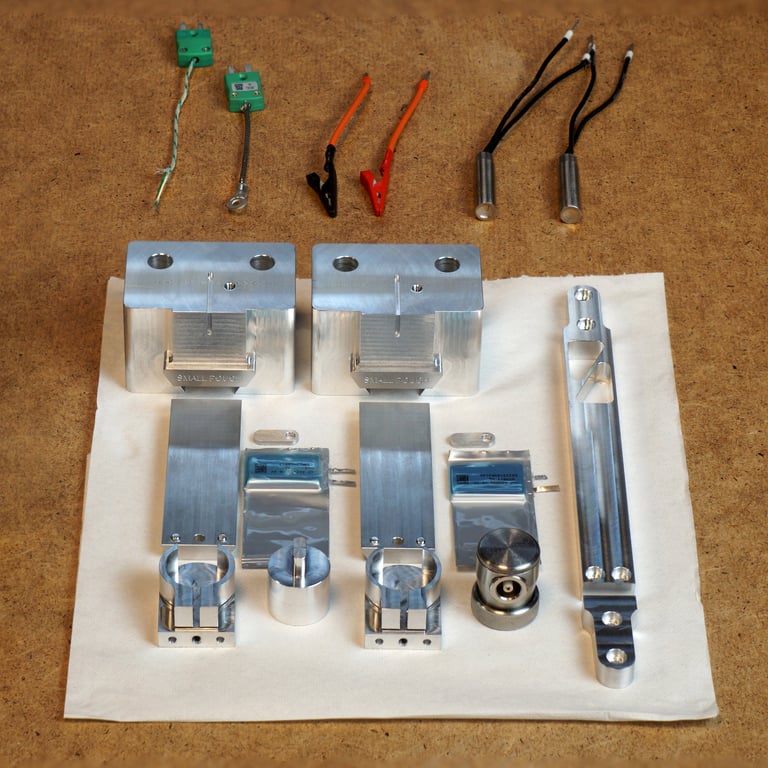
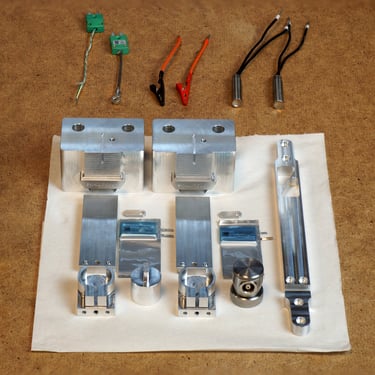
Enclosure can house battery sizes up to 215mm (L) x 110 mm (W) - capacities to be discussed
Sub-assembly for the battery before fitting into enclosure
Aluminium block housing the heating cartridges with thermocouple fixings
Single-cell pouch cells used in this experiment
Interchangable sub-assembly depending on the battery format being tested (cylindrical, pouch, coin cell etc.)
Simple electrical connections to quickly swap damaged connections/sensors
BATTERY HOLDER
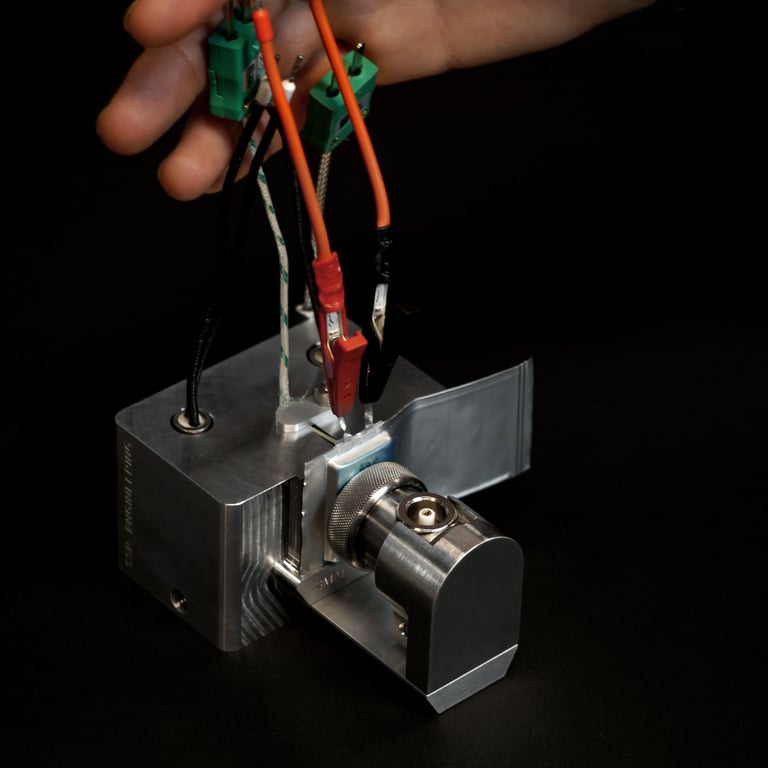
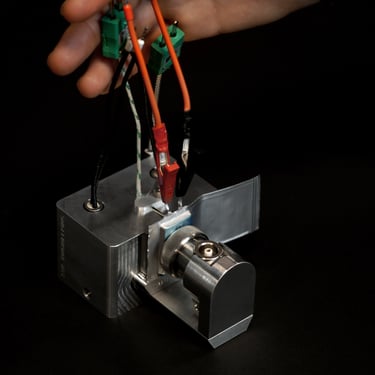
SOFTWARE CONTROL
PID control of heating programmes (manual v.s. heat sink wait)
Visualisation of 3 thermocouple sensors
Automatic heating shut-off when battery thermal runaway detected
Data acquisition
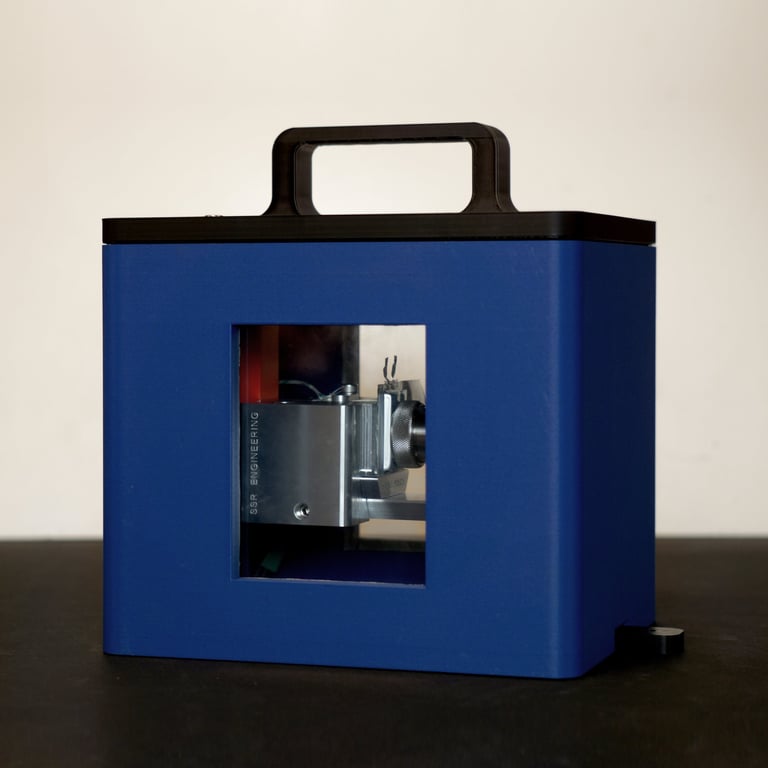
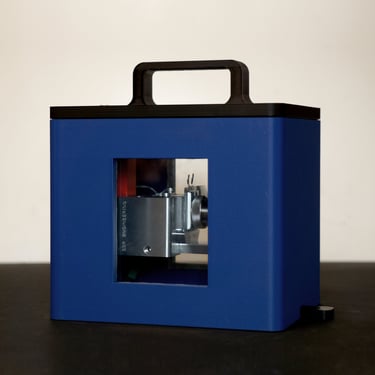
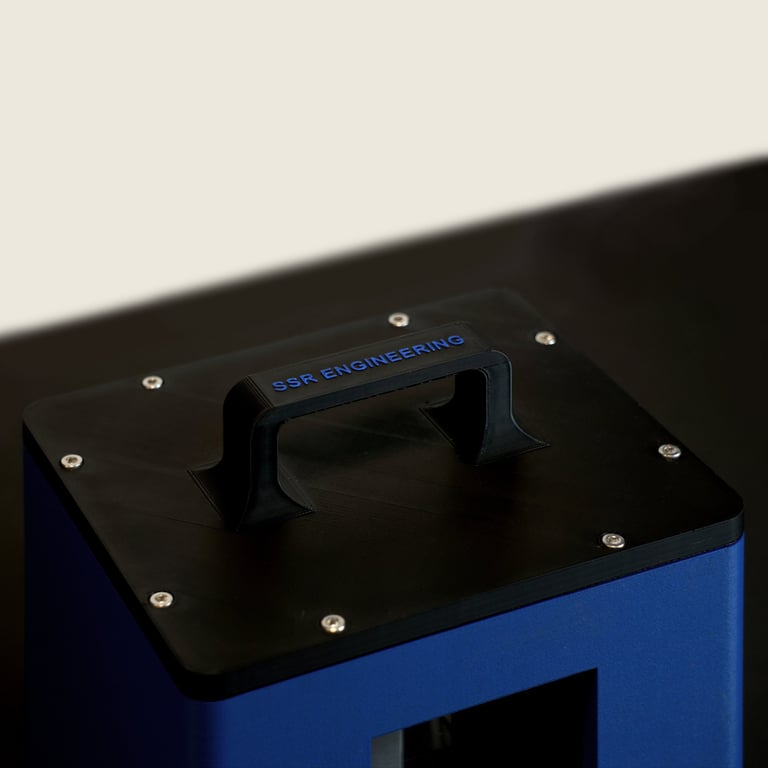
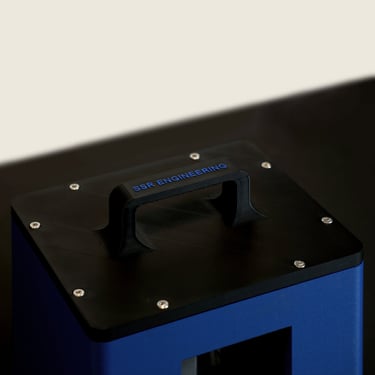
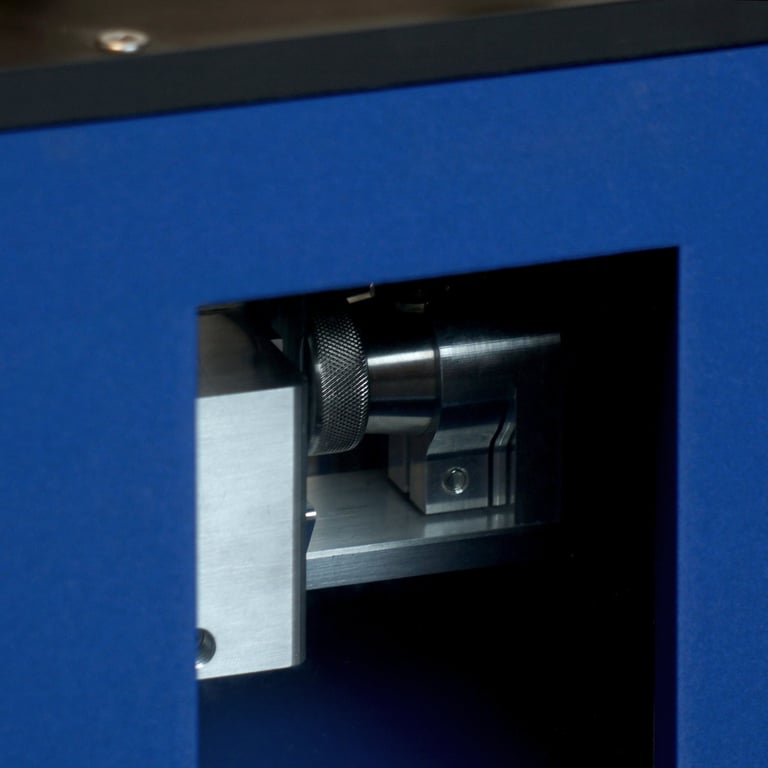
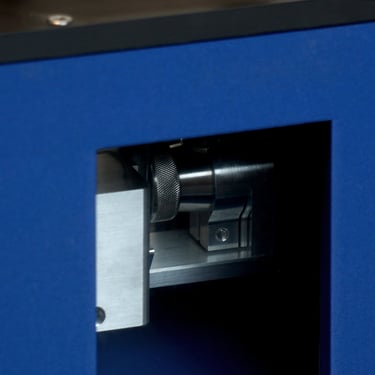
X-RAY DIFFRACTION (XRD) ENCLOSURE
3D-printed enclosure with viewing window - complete battery sub-assembly can be quickly swapped between the high-speed imaging and XRD enclosures.
Get in touch if you are looking for an experimental chamber, or interested in commissioning a bespoke project
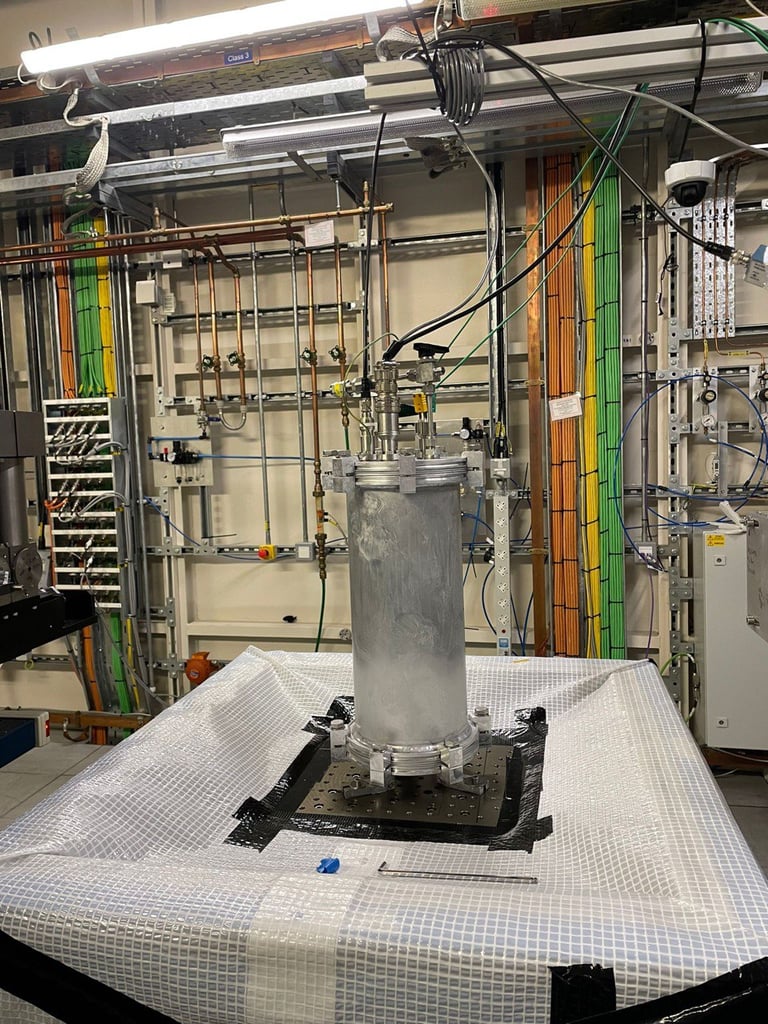
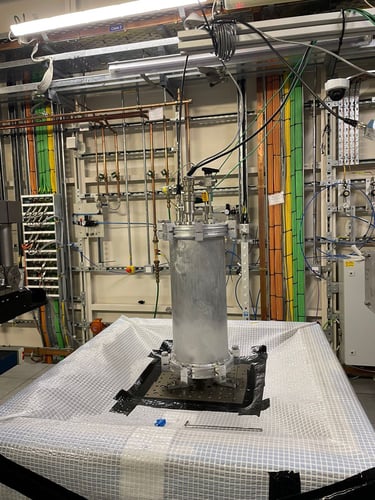
Precision machining partner Minor Detail
© Copyright SSR Systems Engineering Ltd - All rights reserved

